Just How to Avoid Weld Undercut: Important Tips for Welders
Just How to Avoid Weld Undercut: Important Tips for Welders
Blog Article
Recognizing the Causes and Solutions for Undercut Welding in Steel Fabrication Processes
In the world of metal manufacture processes, the event of undercut welding postures a substantial obstacle that requires a detailed understanding of its reasons and sensible services. The complex interaction of numerous variables during welding procedures can cause this undesirable phenomenon, impacting the structural stability and total top quality of the bonded joints - Preventing weld undercut. By studying the source of undercut welding and checking out reliable therapeutic measures, producers can boost the requirement of their workmanship and guarantee the manufacturing of flawless metal components
Common Reasons For Undercut Welding
Frequently neglected in steel fabrication, undercut welding occurs due to different factors that require thorough attention and experience to be efficiently minimized. In addition, improper welding techniques, such as using the wrong welding angle or travel speed, can additionally add to damage development. The selection of welding specifications, such as voltage, existing, and cord feed speed, plays a substantial duty in the incident of undercut welding.
Impact of Incorrect Welding Parameters
Inaccurate welding parameters can dramatically compromise the integrity and top quality of bonded joints in metal fabrication procedures. The impact of incorrect welding specifications manifests in different methods, leading to structural weak points and problems in the welded parts. Meticulous attention to welding specifications is extremely important to make sure the production of high-grade welds with the desired mechanical residential or commercial properties and architectural stability.
Impact of Improper Lantern Angle
Inappropriate lantern angle in welding operations can significantly affect the high quality and honesty of the last weld joints in steel fabrication processes. The lantern angle plays a crucial duty in establishing the warmth input and distribution throughout welding. When the torch angle is inaccurate, problems such as undercutting can emerge. Damaging is a common welding defect where a groove creates along the weld toe, compromising the joint and compromising its structural honesty.
A lantern angle that is also high can lead to inadequate infiltration, insufficient blend, and increased spatter. On the various other hand, a torch angle that is as well shallow can cause excessive infiltration, burn-through, and distortion of the base material. Preventing weld undercut. Correct torch angle is essential for making certain constant weld quality, strength, and look
To avoid undercutting and other issues triggered by inappropriate lantern angles, welders should be trained to keep the proper lantern angle throughout the welding procedure. Regular monitoring and modification of lantern angles during welding can help achieve sound welds with very little defects.
Function of Inadequate Welding Techniques
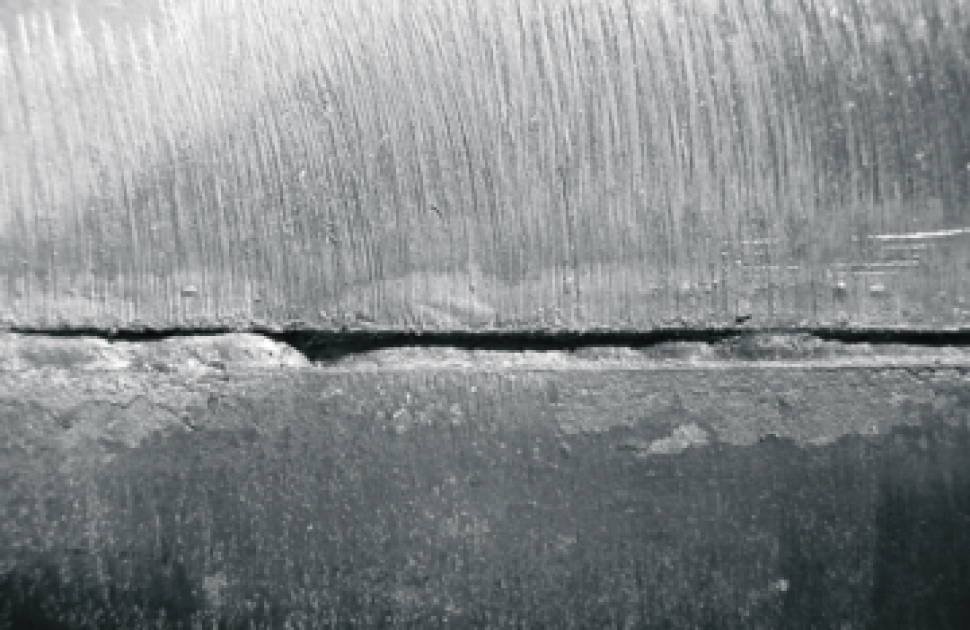
One more element of poor welding strategies is inappropriate weld preparation. Insufficient cleaning of the base metals, wrong joint layout, or insufficient side prep work can all add to damage welding. Insufficient protecting gas coverage or utilizing the incorrect type of gas can result in insufficient fusion and the development of undercut problems.
To deal with the Get the facts role of inadequate welding methods in steel fabrication processes, it is important to give thorough training for welders. Correct education and learning on welding parameters, joint prep work, and securing gas option can help prevent undercut welding and ensure top quality welds in steel manufacture jobs.
Efficient Solutions for Undercut Welding
Resolving undercut welding in metal manufacture calls for applying efficient remedies to improve weld top quality and architectural stability. Among the key services to fight undercut is to change welding specifications such as voltage, current, and travel rate to make sure correct warmth input and combination. By fine-tuning these setups, welders can avoid too much melting of the base metal and filler product, reducing the likelihood of undercut development.
In addition, proper joint prep work is crucial in stopping undercut. Making sure clean base steel surface areas without impurities and utilizing the suitable bevel angle can aid promote far better weld penetration and decrease the risk of undercut - Preventing weld undercut. Utilizing ideal welding methods, such as oscillating the torch or weaving, can also help in distributing warmth equally and filling up the weld joint properly, minimizing the opportunity of undercut flaws
Furthermore, selecting the proper welding consumables, consisting of electrodes and filler steels, is essential in reducing undercut. Utilizing products with ideal chemical structures and mechanical residential properties can contribute to achieving sound welds with marginal undercut. Routine assessment and high quality control measures need to also be implemented to detect and attend to undercut issues without delay, making certain the total honesty of produced steel components.

Verdict
To conclude, recognizing the causes and options for undercut welding in metal construction procedures is crucial for accomplishing high-grade welds. By dealing with usual reasons such as inaccurate welding criteria, incorrect torch angle, and insufficient welding strategies, welders can prevent undercutting and make certain strong, sturdy welds. It is important to pay interest to these variables and carry out reliable services to boost the overall welding procedure and last item quality.
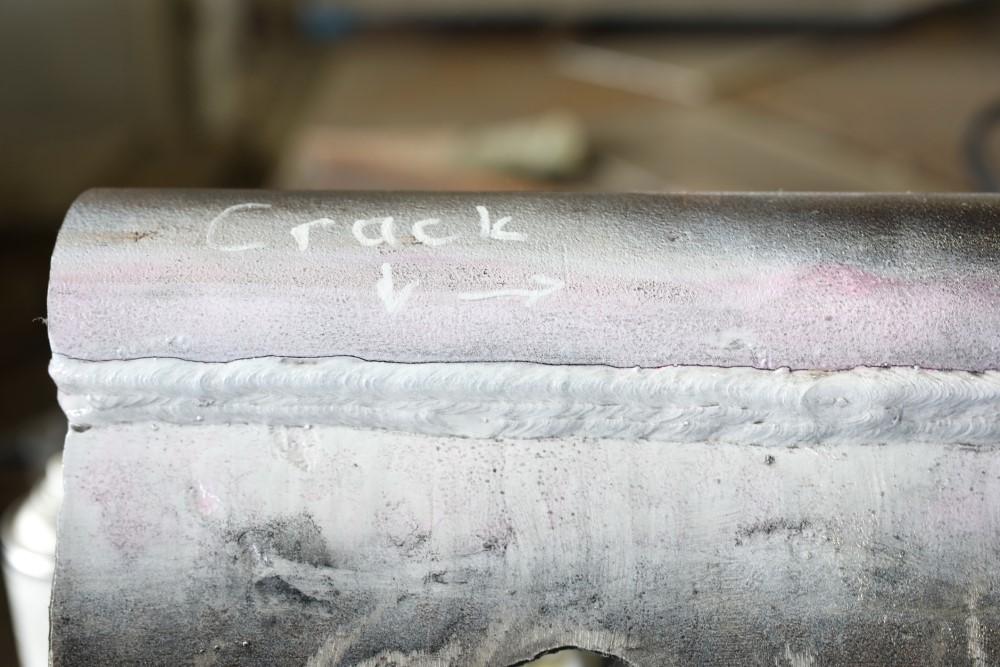
Report this page